ANODIZE
Top provider of NADCAP accredited sulfuric
and hardcoat metal anodizing.
Anodize Overview
Sulfuric Anodizing is a process that provides a conversion on aluminum which changes the surface of the material to a naturally occurring aluminum oxide. The oxides build up changes the surface of the aluminum which then provides greater abrasion resistance as well as increased corrosion protection. Anodize ensures a part can resist corrosion and wear and tear from prolonged use, and that it retains its cosmetic appearance under any conditions.
Anodizing aluminum is an extremely durable post-processing method. Not only does it enhance the properties and appearance of a part, it enables better adhesion for paint primers and glues. This technique utilizes anodic films that provide unique aesthetic effects, such as transparent coatings that reflect light or thick coatings that can absorb dies.
Types Of Anodizing We Provide
Metal Chem Inc. has developed an approved immersion process in full compliance with NADCAP specifications – and provides two types and two classes of electrolytically formed anodic coatings on aluminum and aluminum alloys for non-architectural applications.
Type II & IIB
Sulfuric Acid Anodizing
Sulfuric acid anodizing, conventional coatings produced from sulfuric acid bath. Type II coatings are the result of treating aluminum and aluminum alloys electrolytically in a bath containing sulfuric acid to produce a uniform anodic coating on the metal surface. Anodizing metal removes the conductivity from the part which is required in certain industries like aerospace and military & defense.
Corrosion resistant, available in several color options, and extremely cost effective. Sulfuric anodize coating is a popular service for many of our customers. Sulfuric anodizing yields a coating slightly thinner and less abrasion-resistant surface than hardcoat anodizing.
Excellent Corrosion Resistance
Abrasion Resistance
No Chipping
No Peeling
Metal Chem is proud to provide Type II anodizing as a NADCAP accredited metal plating process for the following specifications:
- MIL-PRF-8625
- MIL-A-8625
- TT-C-490
AC7108/8 – NADCAP Audit Criteria for Anodizing
1000 Series
2000 Series
3000 Series
5000 Series
6000 Series
7000 Series
Sand & Die Cast
MIC 6
Metal Chem offers the following finishes for Type II and Type IIB anodizing:
- Black
- Grey
- Blue
- Green
- Red
- Brown
- Orange
- Olive Drab
- Gold
Type III
Hardcoat Anodizing
Hard anodic coatings are the result of treating aluminum and aluminum alloys electrolytically to produce a uniform anodic coating on the metal surface, this process operation produces a heavy dense coating of specified thickness on aluminum alloys. Type III coatings shall not be applied to aluminum alloys with a nominal copper content in excess of 5.0 percent or nominal silicon content in excess of 8.0 percent. Anodizing metal removes the conductivity from the part which is required in certain industries like aerospace and military & defense.
Metal Chem is proud to provide Type II anodizing as a NADCAP accredited metal plating process for the following specifications:
- MIL-PRF-8625
- MIL-A-8625
- TT-C-490
AC7108/8 – NADCAP Audit Criteria for Anodizing
1000 Series
2000 Series
3000 Series
5000 Series
6000 Series
7000 Series
Sand & Die Cast
MIC 6
Metal Chem offers the following finishes for Type III hard anodizing:
- Black
- Clear
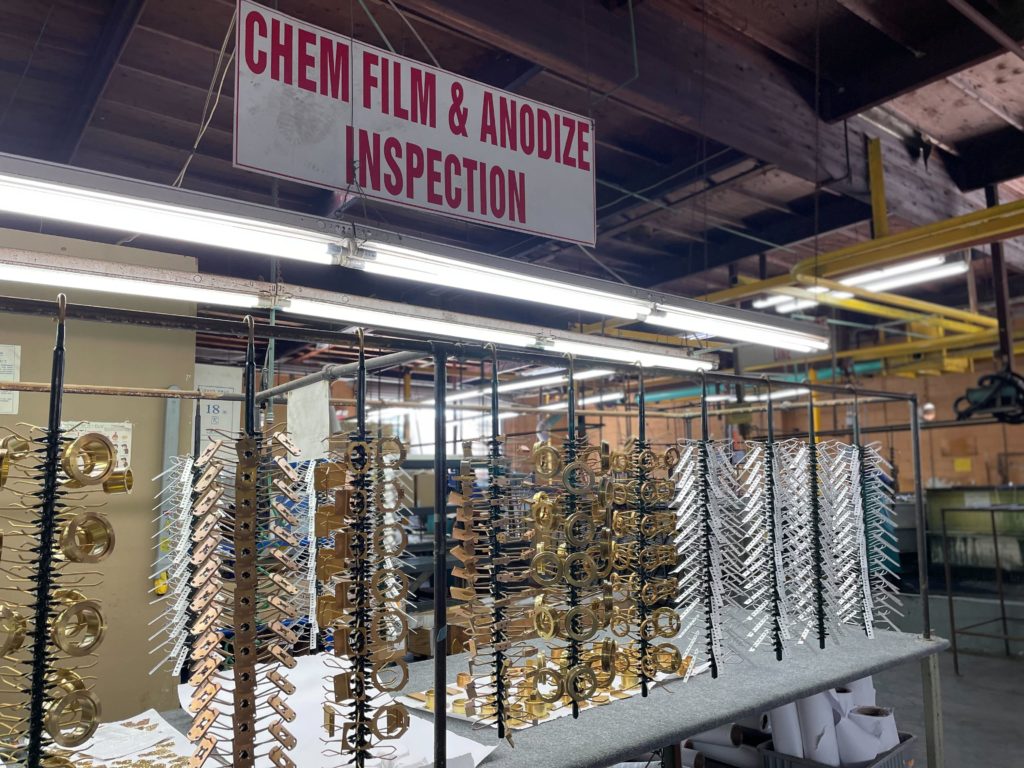
Anodize metal Plating
Quality System
With a facility that boasts over 15,000 square feet, our headquarters includes an in-house laboratory and state-of-the-art technology that’s unparalleled in the metal application industry. You can feel confident that your project is in the hands of experts – our control managers have decades of experience in the science of metal finishing, metal plating, and chemistry.
NADCAP Audit Criteria for Solution Analysis and Testing
- B10 – Adhesion Testing
- B14 – Conductivity Testing
- B16 – Coating Thickness Measurement.
- B21 – Paint Color and Gloss Testing
- B22 – Solvent Resistance Testing
- B23 – Other Testing In Support of AC7108
Anodize Plating Quality Control
From Start To Finish
1
Pretreatment + Masking
At Metal Chem, we take the necessary steps to prep your metal prior to the anodizing application. If masking is required, our team includes dedicated experts that handle the masking in-house.
2
Metal Application
Metal Chem Inc. maintains the appropriate process controls for our chemical conversion and electroplating processes which require titration, coating weights, pH, and TDS verification.
3
QA Inspection
Metal Chem uses sophisticated process controls and analysis to ensure all of our final products meet the standards of our accreditations and mil-spec testing validation requirements.
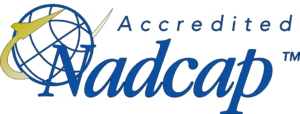
Who We Help
Aerospace & Military Metal Applications Approvals
Since 1991, Metal Chem Inc. has become one of the premiere metal plating and finishing companies in the country. Our NADCAP accreditation has allowed us to proudly fulfill the metal application needs of top technology pioneers in the aerospace, military and naval industries. As an industry leader in spec plating and metal finishing, our team has decades of experience handling complex projects that require a sophisticated level of detail.
Industries We Serve
You ask, we answer
Find answers to the most frequently asked questions about the anodizing process.
Sulfuric Anodizing is a process that provides a conversion on aluminum which changes the surface of the material to a naturally occurring aluminum oxide. The oxides build up changes the surface of the aluminum which then provides greater abrasion resistance as well as increased corrosion protection. Anodize ensures a part can resist corrosion and wear and tear from prolonged use, and that it retains its cosmetic appearance under any conditions.
Yes. Metal Chem is proud to provide Type II anodizing as a NADCAP accredited metal plating process for the following specifications:
- MIL-PRF-8625
- MIL-A-8625
- TT-C-490
AC7108/8 – NADCAP Audit Criteria for Anodizing
Type III (hardcoat) anodizing is thicker and denser than Type II (sulfuric acid), so it isn’t usually dyed. Where Type III anodize is utilized most is for wear-resistance purposes.
Anodizing is a valuable metal application across a variety of industries including:
- Automotive
- Aerospace and defense
- Industrial & Commercial
- Medical
- Robotics
- Energy
Get in Touch
Phone
(818) 727-9951
info@metalcheminc.com
Address
21514 Nordhoff Street
Chatsworth, CA 91311