Amercoats &
Marine Coats
Marine Coats & Amercoat liquid paints.
Marine Coats & Amercoats Overview
Amercoats are high-performance epoxy coatings forming a tough, abrasion-resistant, durable film. These coatings adhere to bare steel, coated steel and inorganic zinc silicate primed surfaces on new construction, repair and field maintenance projects for infrastructure and marine applications. In addition, Metal Chem Inc. also offers Amercoat One coating system, which has the same chemical and corrosion resistance as traditional two-component epoxy coatings, and it can be used as an intermediate coating over inorganic and organic zinc-rich primers, or as a direct-to-metal (DTM) primer in multilayer coatings systems. It is well-suited to a variety of chemical, petrochemical, infrastructure, marine, mining and power industry applications.
Marine Coats & Amercoats Liquid Paint details
Marine Coats provide protection for equipment used in demanding conditions and environments. Metal Chem Inc. has helped coat a wide variety of projects in various markets including the marine and infrastructure industry.
Amercoat® products provide the confidence of heavy duty protection against chemical contact, corrosion, abrasion, and impact damage in the harshest of end use environments. Segments demanding heavy protective performance often include Transportation, Oil and Gas, Mining, Agricultural and Construction Equipment, and Industrial Machinery.
Amercoats can also provide outstanding protection and durability while minimizing steps and layers, saving both time and money during the application process. Additionally, Amercoat products are designed to be forgiving and easy to apply even on large, complex surfaces while meeting national and local VOC regulations.
Product Data
•Outstanding resistance to chemicals and severe weathering
•Excellent adhesion to inorganic zincs
•Easily applied by airless or conventional spray •Amercoat 861 Accelerator can be used for low temperature curing.
• See product data sheet.
Typical Uses
Amercoat 68HS is a shop primer for bare steel on new construction or major repair projects, and as a field maintenance primer over bare steel or steel coated with organic or inorganic zinc primers and epoxy topcoats such as, Amercoat 385, Amerlock® 400 or AmershieldTM. Amercoat 68HS may be used to repair itself or inorganic zinc primers.
The Amercoat 240 Series features surface tolerant, direct-to-metal universal epoxies with excellent wetting and edge covering characteristics. Now you have a single product that is able to replace a series of specialized coatings with a one-coat application that can be used in a wide range of marine and protective environmental and application conditions.
Amercoat® 240 Features
• Superior edge retention & less stripe coating
• High build (up to 12 mils) in one coat
• Direct-to-metal application
• Self-priming and surface tolerant
• Excellent adhesion to tight rust
• Fast dry-to-recoat and rapid handling properties
• Abrasion resistant
• Exceptional corrosion protection
• Very low VOC
Amerlock is the high-solids (85%), high-build epoxy protective coating that provides the solution to maintenance painting in tough industrial, marine and offshore environments around the world.
A tough durable coating
There is an Amerlock coating for every maintenance job. It provides durable, dependable protection from chemicals and corrosion in a variety of industrial and infrastructure applications and excellent resistance to weather, moisture and chemical fumes.
Solve complex corrosion problems with minimal preparation
These coatings are designed to permit application directly to tightly adhering rust and intact old paint without blast cleaning. Amerlock has superior wetting action and creates a tight bond to the underlying metal. Amerlock’s low-solvent formula will typically not lift or wrinkle paint and it is also an excellent direct-to-metal protective coating for new, unpainted surfaces.
Compatible with a wide range of topcoats
It is a self-priming topcoat over most existing coatings. It can be overcoated with a wide range of other PPG topcoats if desired for extended weatherability or special situations. Amerlock 400 cures through a wide temperature range and is available in a variety of colours.
General maintenance applications
Its chemical resistance to splash/spillage, fumes and immersion in neutral, fresh and salt water makes Amerlock 400 an excellent choice for a wide variety of general maintenance applications.
Faster drying time
Choose Amerlock 2 for its faster drying time. It is dry to touch in as few as 3 hours at 20°C (dependant on film build) and can be recoated in 6 hours.
It also offers the least amount of odour, low temperature cure down to -10°C, superior chemical resistance and high surface tolerance for excellent adhesion, making Amerlock products the choice of maintenance professionals worldwide.
Amerlock can be used on:
- concrete floors
- roofs
- bridges
- production areas
- tank exteriors
- oil tanks
- showrooms
- marine weathering
- offshore
- vehicle workshops
- piping
- water towers
DESCRIPTION
Two-component, high solids epoxy coating. See product data sheet.
PRINCIPAL CHARACTERISTICS
• High performance self priming universal epoxy
• High solids, low VOC
• Surface tolerant and abrasion resistant
• Compatible with prepared, damp surfaces
• Good adhesion on most existing coatings
• Available in MIO or conventional pigmented grade
• Good resistance to splash and spillage of chemicals
DESCRIPTION
Two-component, high solids epoxy coating. See product data sheet.
PRINCIPAL CHARACTERISTICS
• Low-temperature curing down to 0°C (32°F)
• High performance self priming universal epoxy
• High solids, low VOC
• Surface tolerant and abrasion resistant
• Compatible with prepared, damp surfaces
• Good adhesion on most existing coatings
• Good resistance to splash and spillage of chemicals
• Meets NSF Standard 61 for tanks, pipes, valves and fittings (US manufacturing only)
• Proven coating as a bulk rail lining and DTM exterior coating
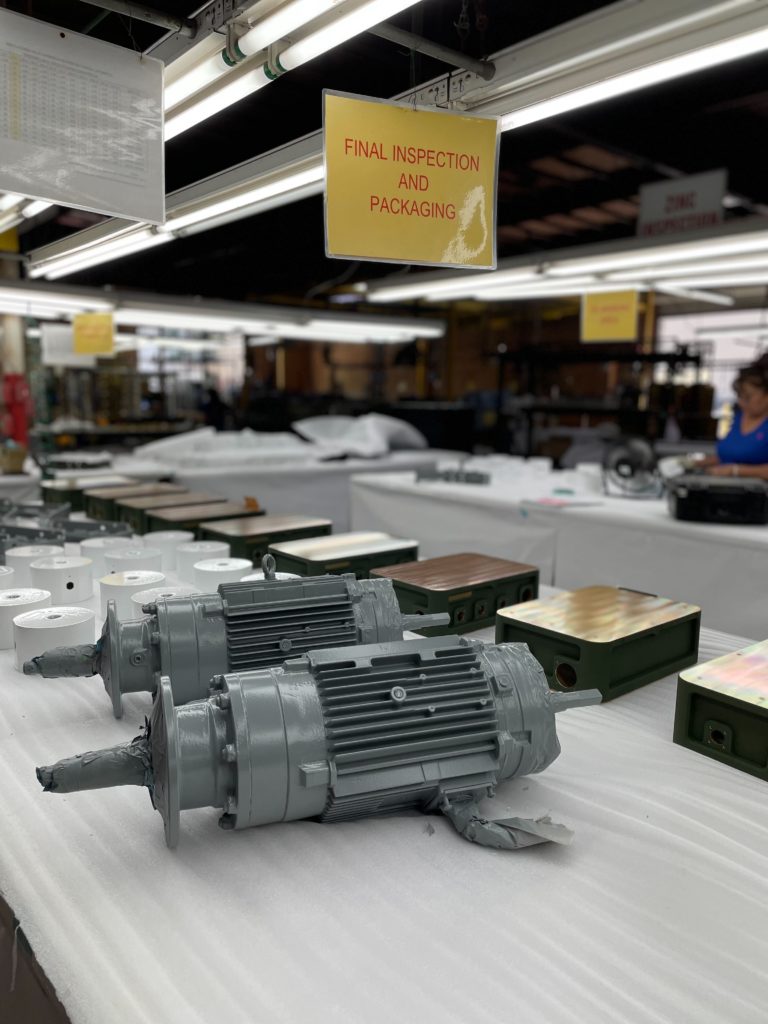
Marine Coat & Amercoats
Quality System
With a facility that boasts more than 15,000 square feet, our headquarters includes an in-house laboratory and state-of-the-art technology that’s unparalleled in the metal application industry. You can feel confident that your project is in the hands of experts – our team of control managers has decades of experience in the science of metal finishing, metal plating, and chemistry.
QUALITY CRITERIA FOR SOLUTION ANALYSIS AND TESTING
- B10 – Adhesion Testing
- B14 – Conductivity Testing
- B16 – Coating Thickness Measurement.
- B21 – Paint Color and Gloss Testing
- B22 – Solvent Resistance Testing
- B23 – Other Testing In Support of AC7108
Amerlock & Amercoats Quality Control
From Start To Finish
1
Metal Prep + Masking
At Metal Chem, we take the necessary steps to prep your metal prior to the marine coating application. If masking is required, our team includes dedicated experts that handle the masking in-house.
2
Metal Application
Metal Chem Inc. maintains the appropriate process controls for our chemical conversion and electroplating processes which require titration, coating weights, pH, and TDS verification.
3
QA Inspection
Metal Chem uses sophisticated process controls and analysis to ensure all of our final products meet the standards of our accreditations and mil-spec testing validation requirements.
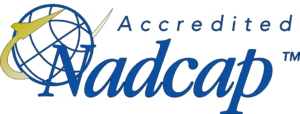
Who We Help
Aerospace & Military Metal Applications Approvals
Since 1991, Metal Chem Inc. has become one of the premiere metal plating and finishing companies in the country. Our NADCAP accreditation has allowed us to proudly fulfill the metal application needs of top technology pioneers in the aerospace, military and naval industries. As an industry leader in spec plating and metal finishing, our team has decades of experience handling complex projects that require a sophisticated level of detail.
Industries We Serve
You ask, we answer
Find answers to the most frequently asked questions about the marine coat process.
There are countless benefits to using Amercoats for your metal application project. However, the most important features are as follows:
- Excellent film hardness and durability
- Corrosion and chemical resistance
- Full complement of VOC compliant offerings
- Equipment and machinery operating in harsh environments
- Large, complex structures and surfaces
- Blast prepared substrates
Marine Coats provide protection for equipment used in demanding conditions and environments. Metal Chem Inc. has helped coat a wide variety of projects – using Amercoats & Amerlocks – in various markets including the marine and infrastructure industry.
Metal Chem Inc is proud to include approvals for marine coatings from Lockheed Martin, Northrop Grumman, and more.
Get in Touch
Phone
(818) 727-9951
info@metalcheminc.com
Address
21514 Nordhoff Street
Chatsworth, CA 91311